Stalling in rotary drilling machines can lead to significant downtime and delays in your project. Understanding the causes of stalling is crucial for effective rotary drilling machine troubleshooting and optimizing machine performance. This article explores the most common factors contributing to stalling in rotary drilling rigs and provides practical solutions to help you troubleshoot efficiently.
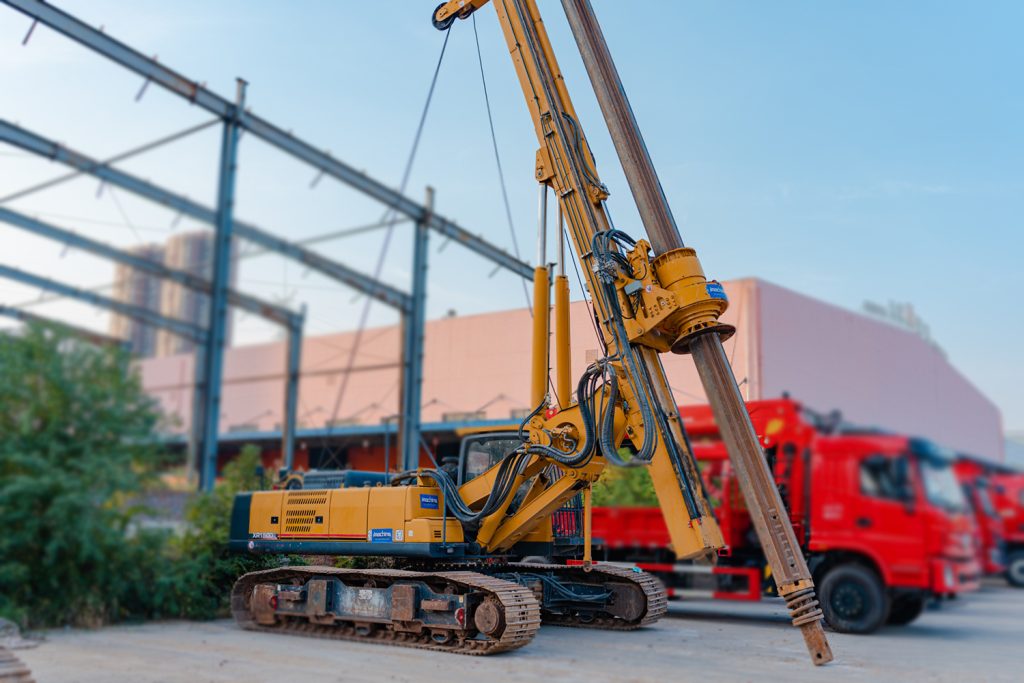
Common Causes of Stalling in Rotary Drilling Machines
- Broken Wings on Drill Bits
A common issue that causes stalling in rotary drilling machines is the breakage of wings on drill bits. This can lead to a significant decrease in drilling efficiency. To minimize this problem, it’s essential to address it quickly. The introduction of seamless pipes lubricated with butter or asphalt can help extract broken wings more efficiently. Ensure the bottom of the hole is cleared of rock debris before retrieval, using a thorough air blow.
- Increased Diameter of Newly Installed Drill Bits
Stalling often occurs when newly installed drill bits have a larger diameter than the original ones. To manage this, apply gradual pressure during the chiseling process and increase the thrust force incrementally to reach optimal working pressure. This method will allow the rotary drilling machine to function smoothly without stalling.
- Machine Displacement or Tool Misalignment
During the chiseling process, machine displacement or tool misalignment can lead to stalling. To prevent this, ensure operational diligence, especially during prolonged drilling pauses. Regularly clear rock powder and lift the drill tools to avoid burying the impactor in debris. This simple maintenance step can reduce the chances of stalling and enhance rotary drilling machine performance.

- Rock Debris or Fractures During Chiseling
Stalling can also be caused by falling rocks or encountering fractures and cavities in the rock. In such cases, adjust the torque, use auxiliary tools, and maintain consistent air pressure to lift and rotate the drill tools. These actions help resolve obstructions and avoid stalling during the chiseling process.
- Difficulty in Dust Disposal in Stony Areas
In muddy or stony regions, efficient dust disposal becomes more challenging, leading to operational stalling. Implement effective dust removal mechanisms to ensure the drill bit continues working without clogging, promoting smooth and uninterrupted drilling operations.
- Operational Negligence
Neglecting operational best practices, such as failing to clear rock powder during extended drilling pauses, can lead to stalling in rotary drilling rigs. To avoid this, always follow the recommended procedures, ensuring timely cleaning and lifting of drill tools to prevent the impactor from being buried under rock debris.

Solutions for Overcoming Stalling Issues
When facing severe stalling where drill tools cannot be lifted or lowered, and the impactor is unresponsive, apply additional torque or enlist auxiliary tools. Simultaneously provide air pressure while gradually elevating the drill tools to resolve the malfunction. This approach can help overcome common stalling problems effectively.
By identifying the common causes of stalling in rotary drilling machines and employing efficient troubleshooting strategies, you can maintain optimal rotary drilling machine performance. Implementing these solutions will ensure smooth and efficient drilling operations, preventing delays and improving productivity on your drilling projects.
Looking for Quality Rotary Drilling Machines for Sale?
If you’re in the market for rotary drilling machines for sale, consider investing in high-quality, well-maintained machinery to reduce the likelihood of stalling and ensure optimal performance. A properly maintained machine will contribute to more efficient drilling, higher uptime, and ultimately, a better return on investment.