Understanding Wear Parts in Concrete Pumps: What Contractors Need to Know
Concrete pump wear parts are critical components in modern construction machinery, especially in equipment designed to deliver concrete efficiently and accurately across job sites. These parts endure immense pressure and constant abrasion during operation, making them particularly vulnerable to wear and tear. Whether utilizing a boom pump or a trailer-mounted unit, understanding which components wear out the fastest—and how often they should be replaced—is essential for maintaining uptime, ensuring safety, and managing costs effectively.
Yet, many buyers remain fixated solely on the upfront concrete pump price, overlooking the cumulative maintenance expenses tied to wear parts. These hidden costs can quietly erode profitability if not properly managed.
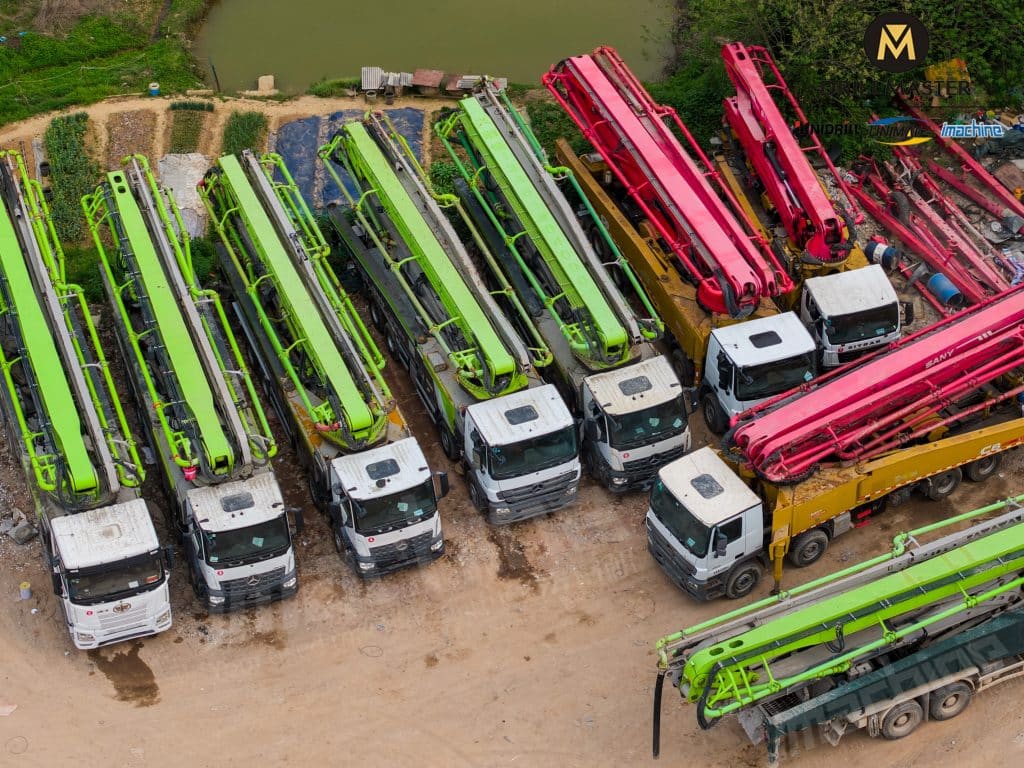
Why Wear Parts Demand Attention in Pump Maintenance
Wear parts are high-impact components, enduring intense friction and pressure during every pumping cycle. As concrete rushes through the system, it grinds against valves, plates, seals, and cylinders—slowly but inevitably eroding them.
Neglecting these parts doesn’t just reduce efficiency—it risks serious mechanical failure and unscheduled downtime. Consistent monitoring and timely replacements are non-negotiable in a preventative maintenance strategy.
The Most Frequently Replaced Concrete Pump Wear Part
1. Wear Plate & Cutting Ring
These components form the seal that allows the pump to alternate between cylinders. The Wear Plate absorbs continuous abrasive stress, while the Cutting Ring maintains pressure-tight contact.
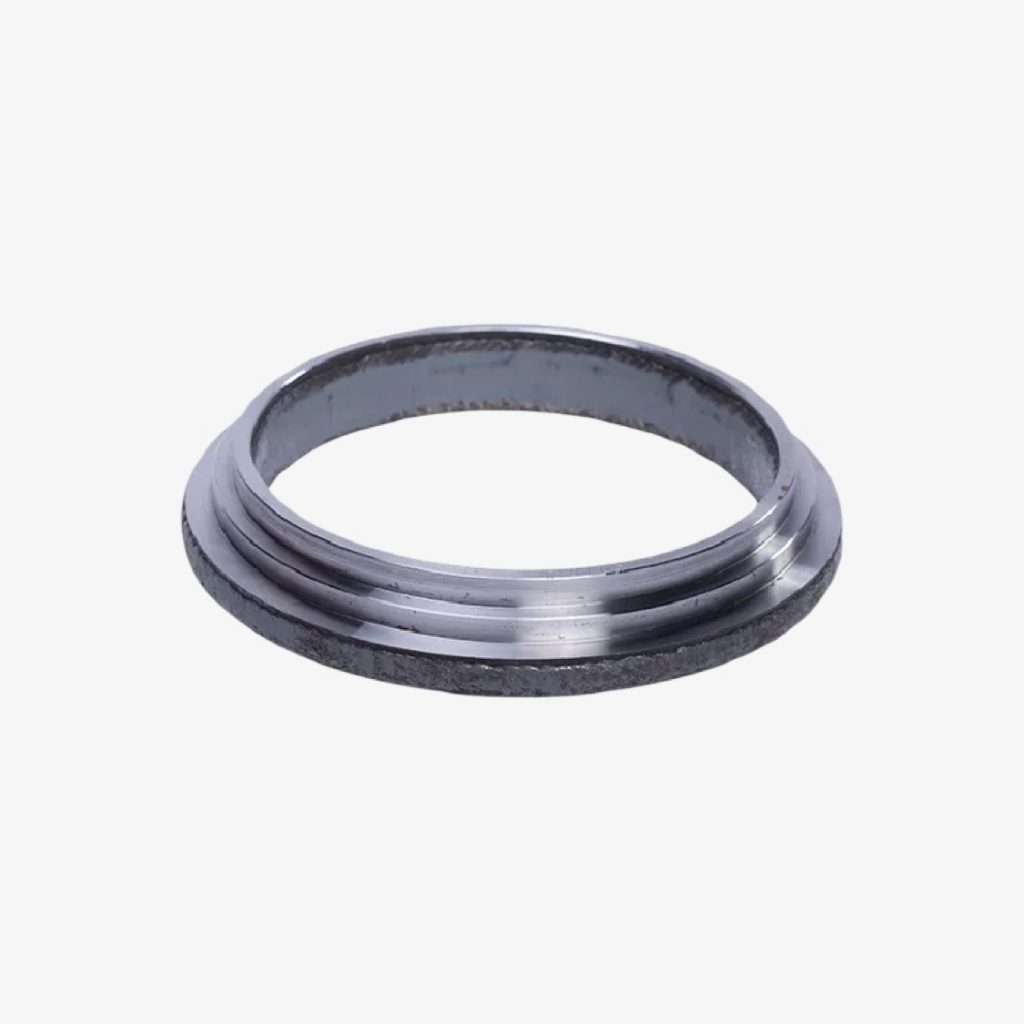
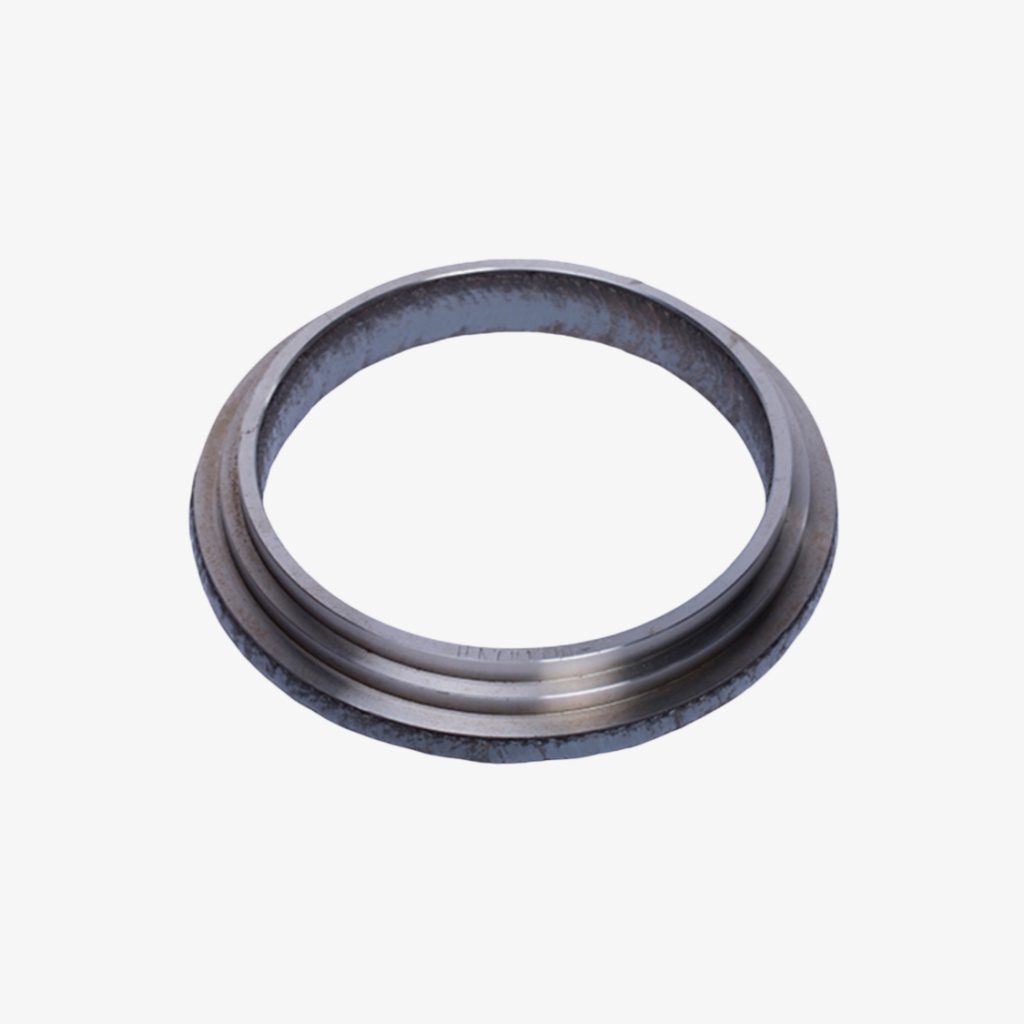
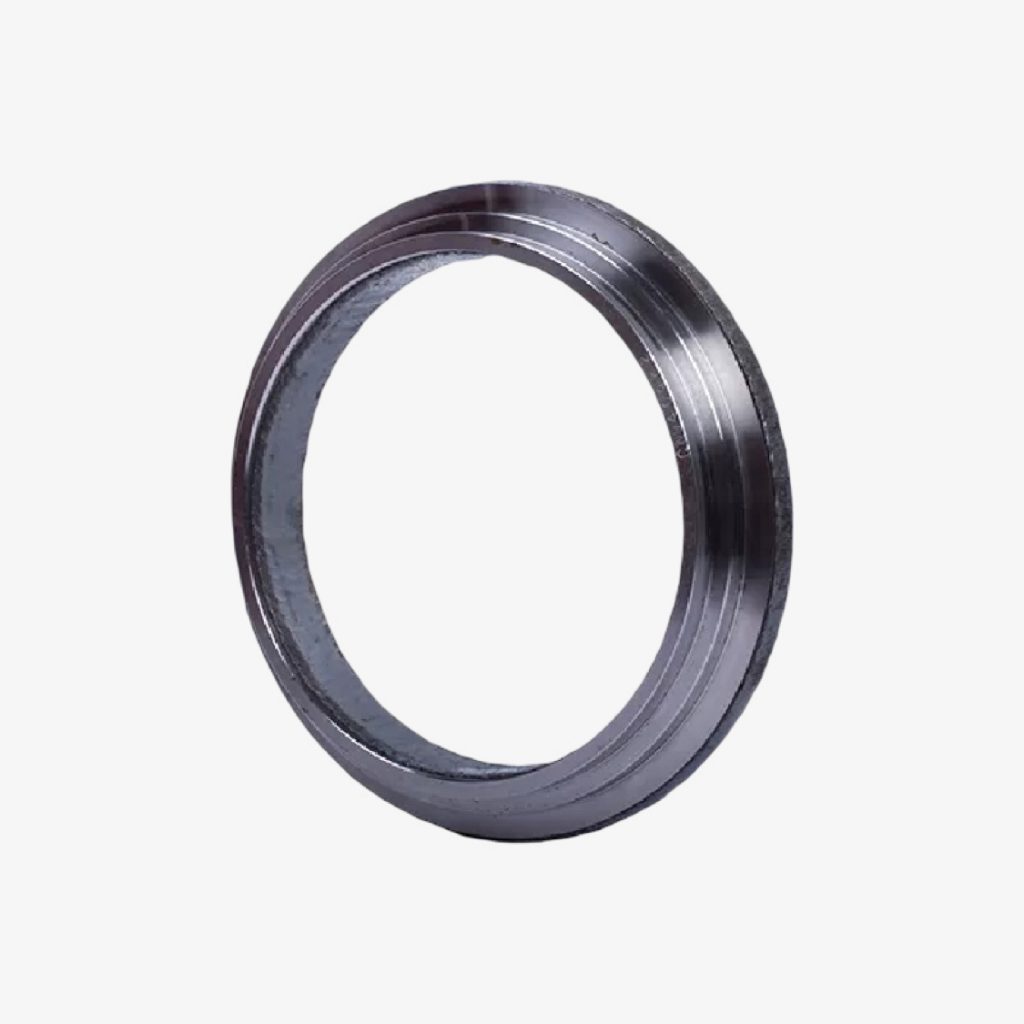
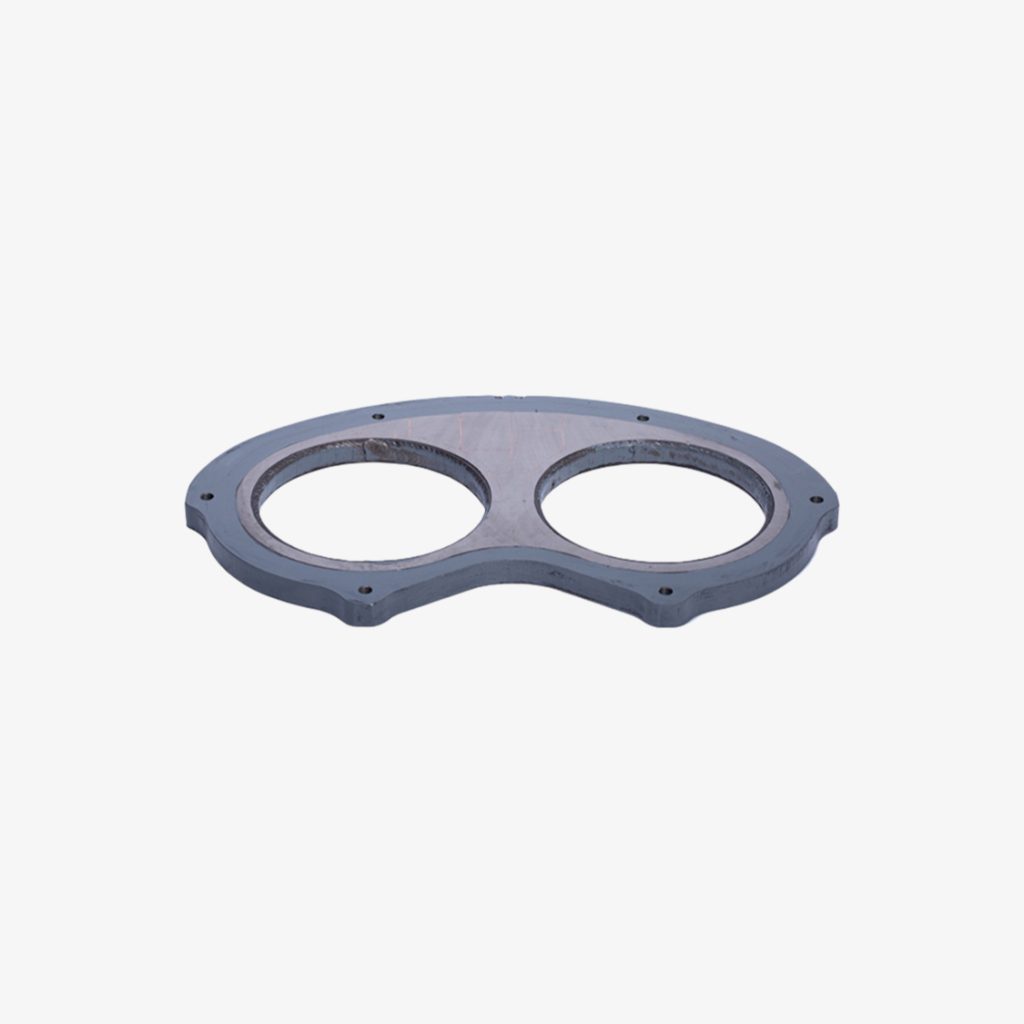
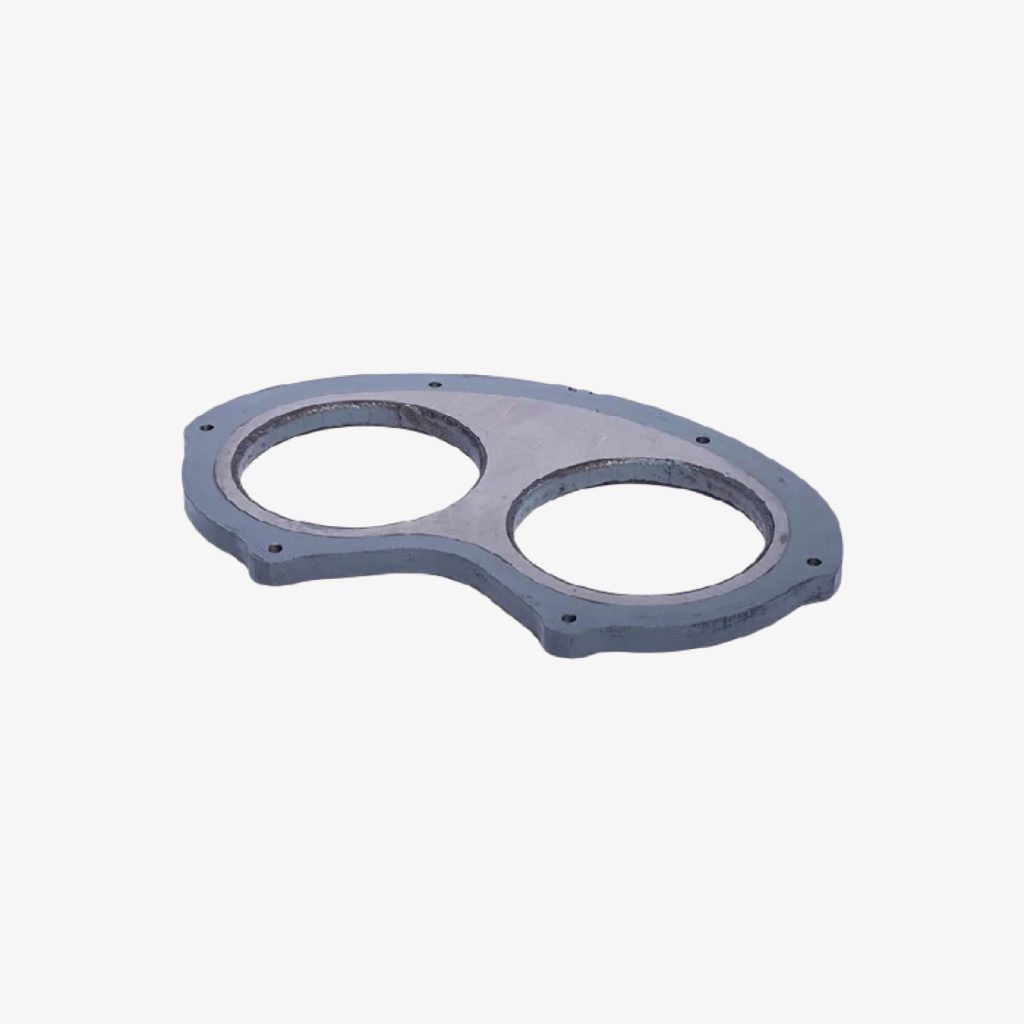
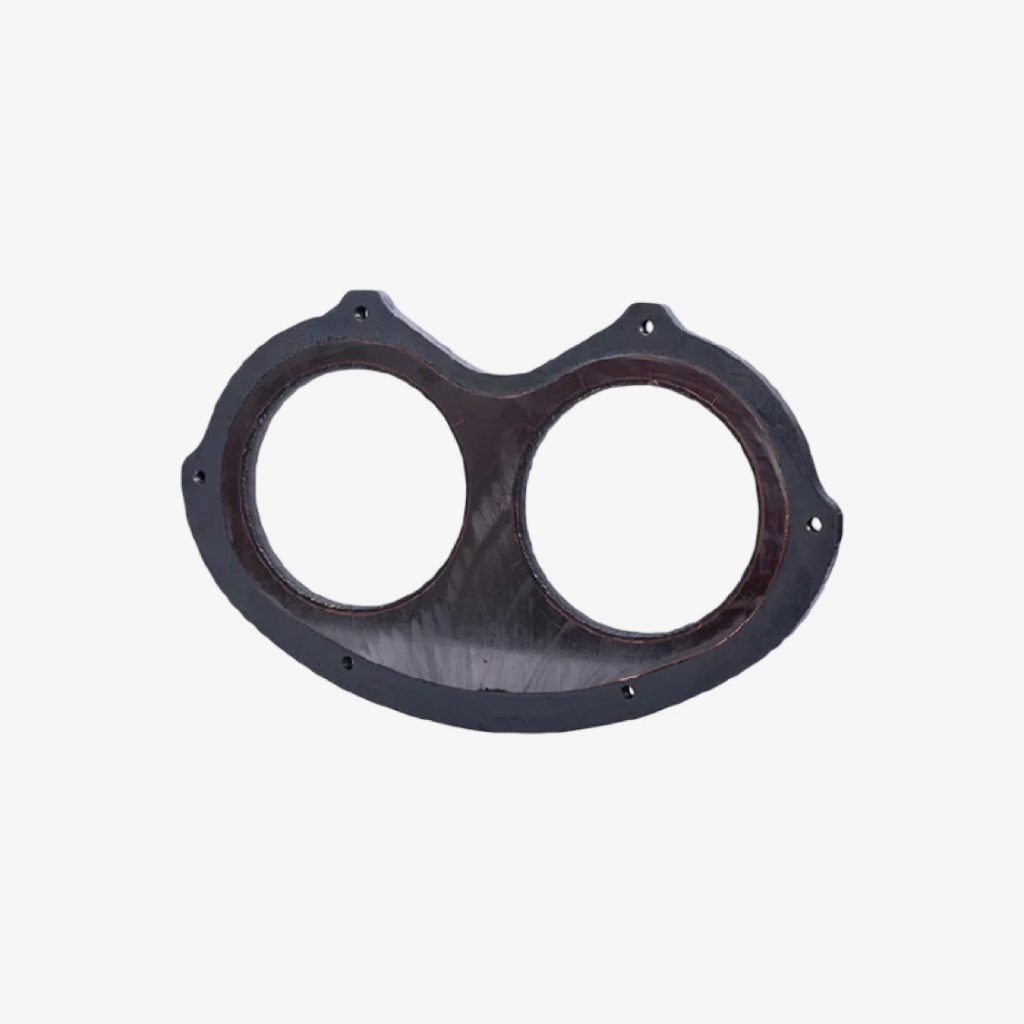
- Replacement Frequency: Every 300–500 operating hours, depending on material abrasiveness.
2. Concrete Pistons (Piston Cups)
These rubber or polyurethane components also known as the Piston Seal, drive the concrete through the pump cylinder. They endure constant pressure and friction.
- Replacement Frequency: Every 600–800 hours; sooner in challenging pumping conditions.
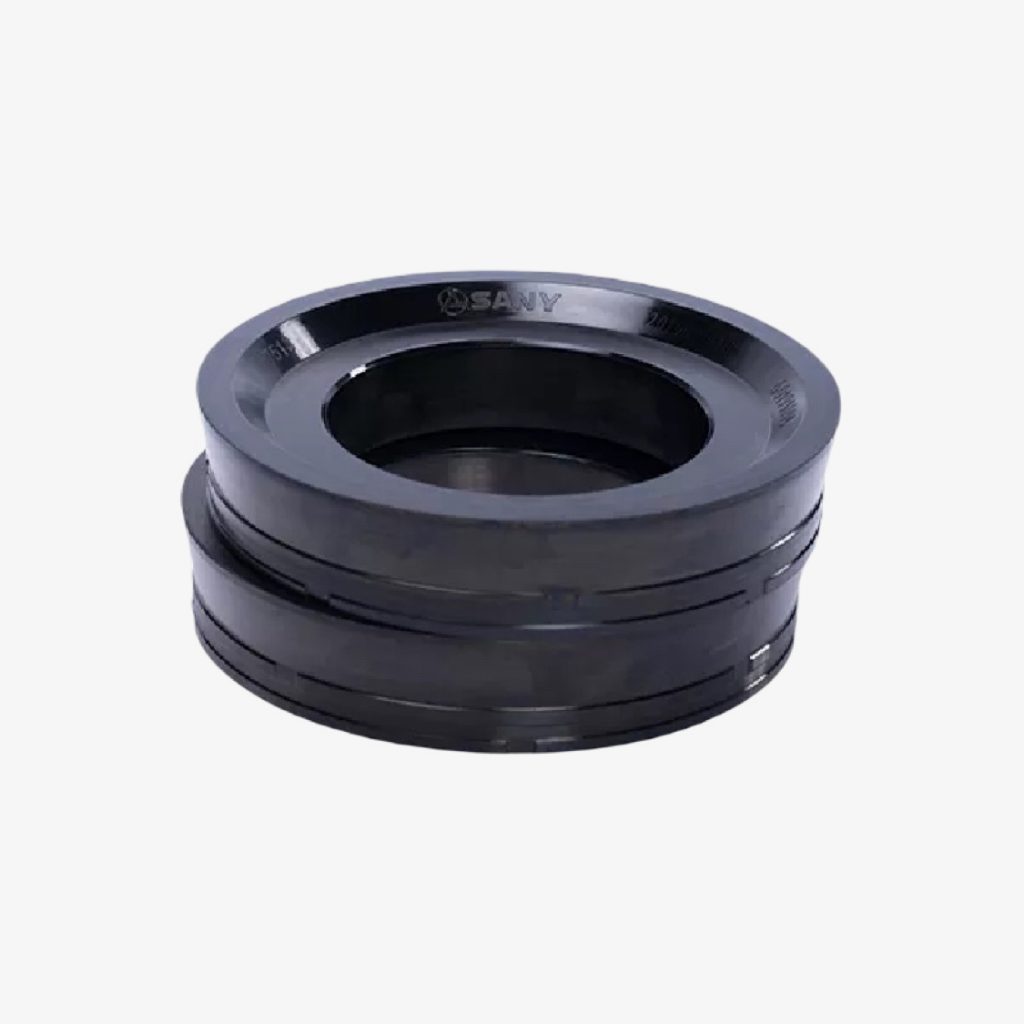
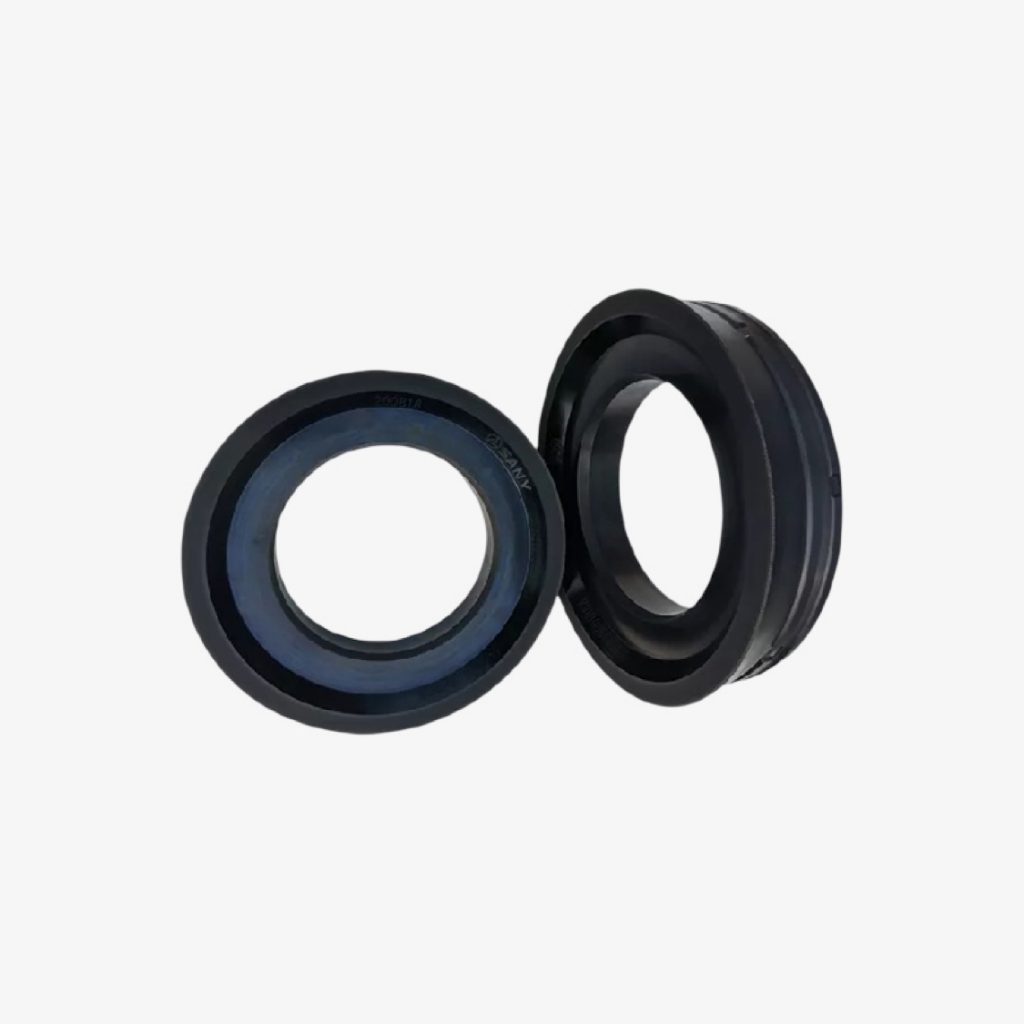
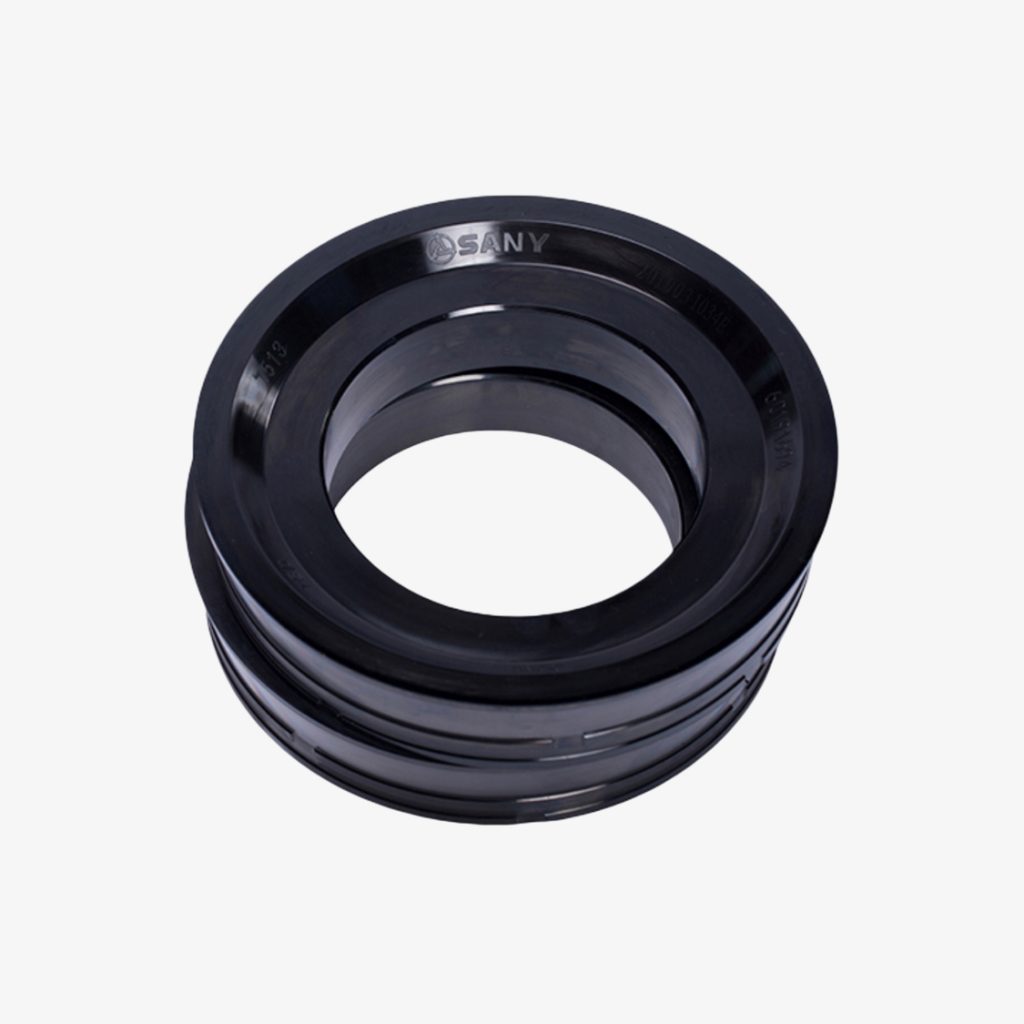
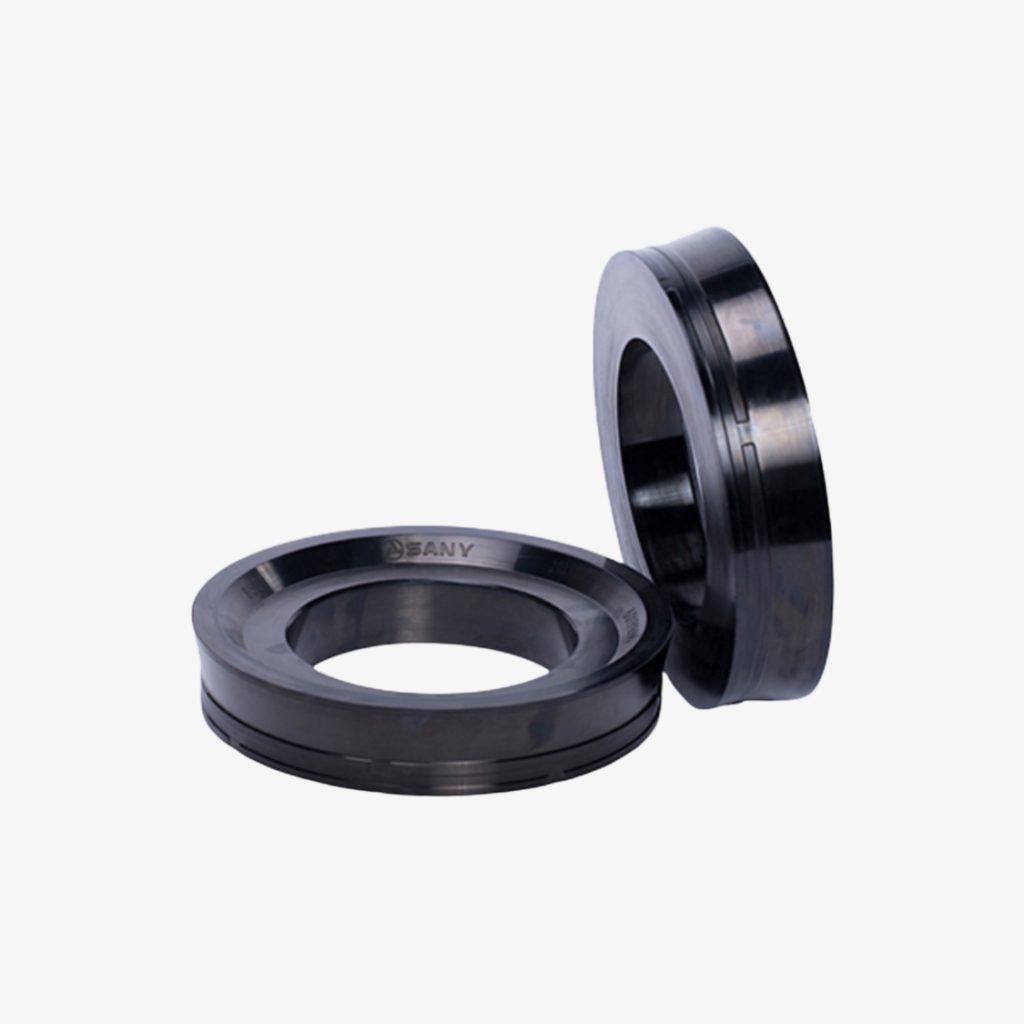
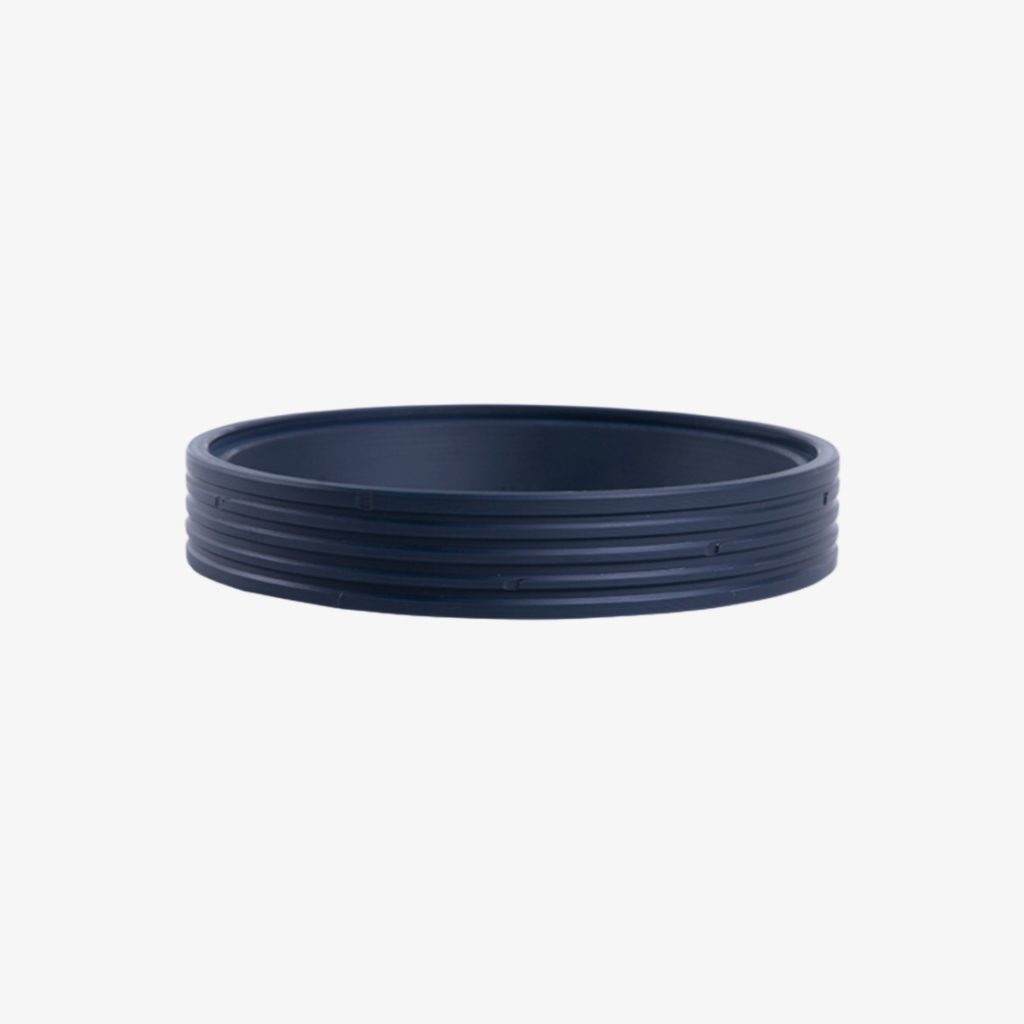
3. S-Valve or Swing Tube
Crucial to switching concrete flow between cylinders, the S-valve faces both rotational stress and abrasive erosion.
- Replacement Frequency: Approximately every 1,000–1,500 hours.
4. Delivery Cylinders
These are responsible for channeling concrete under high pressure. Over time, the Delivery Cylinder‘s internal walls thin and weaken due to abrasion.
- Replacement Frequency: Every 1,500–2,000 hours, depending on material flow and pressure levels.
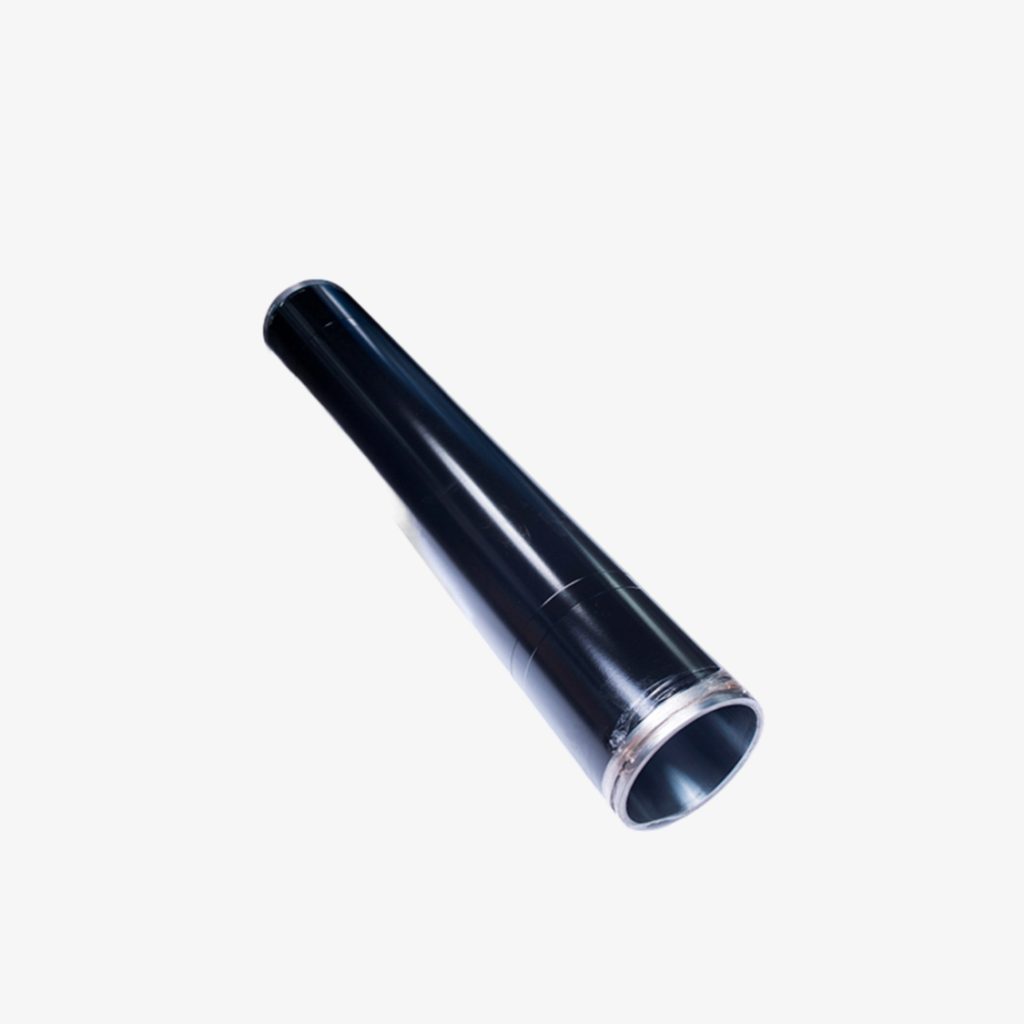
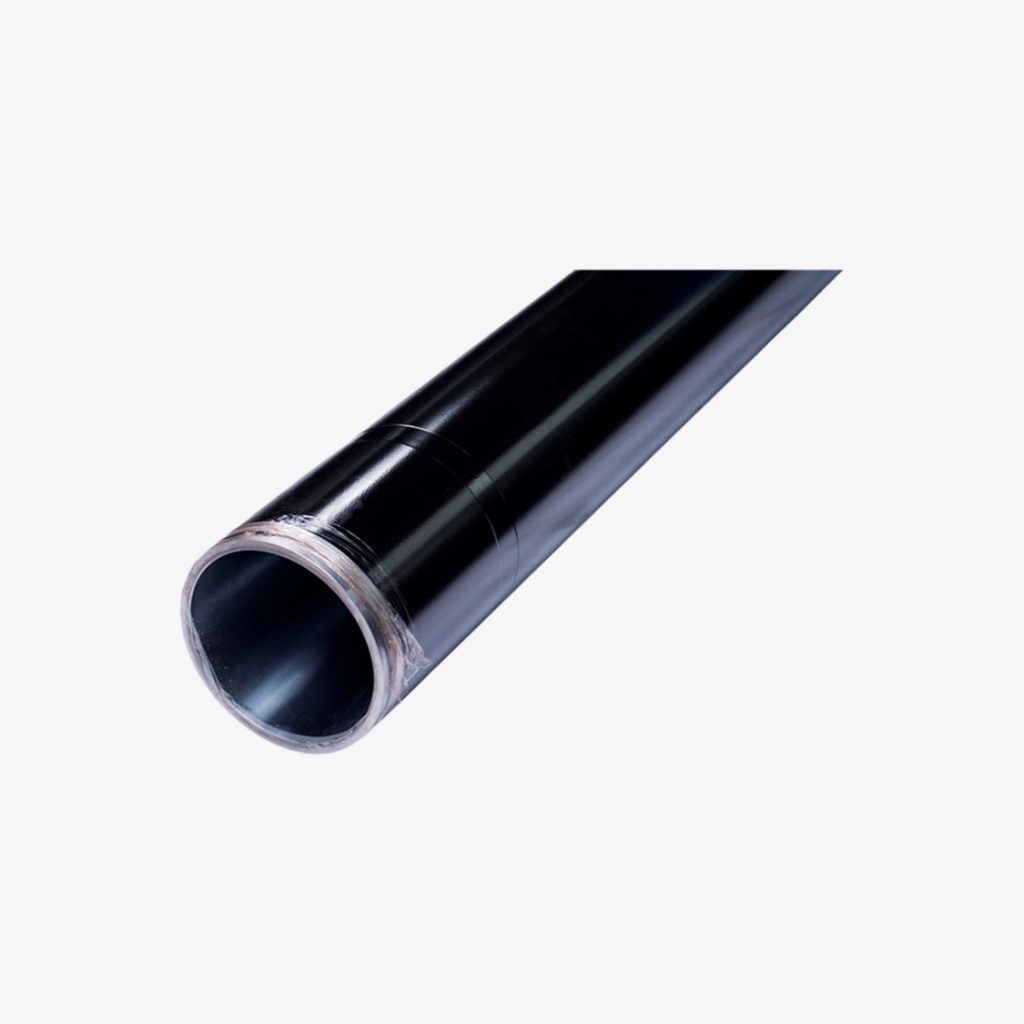
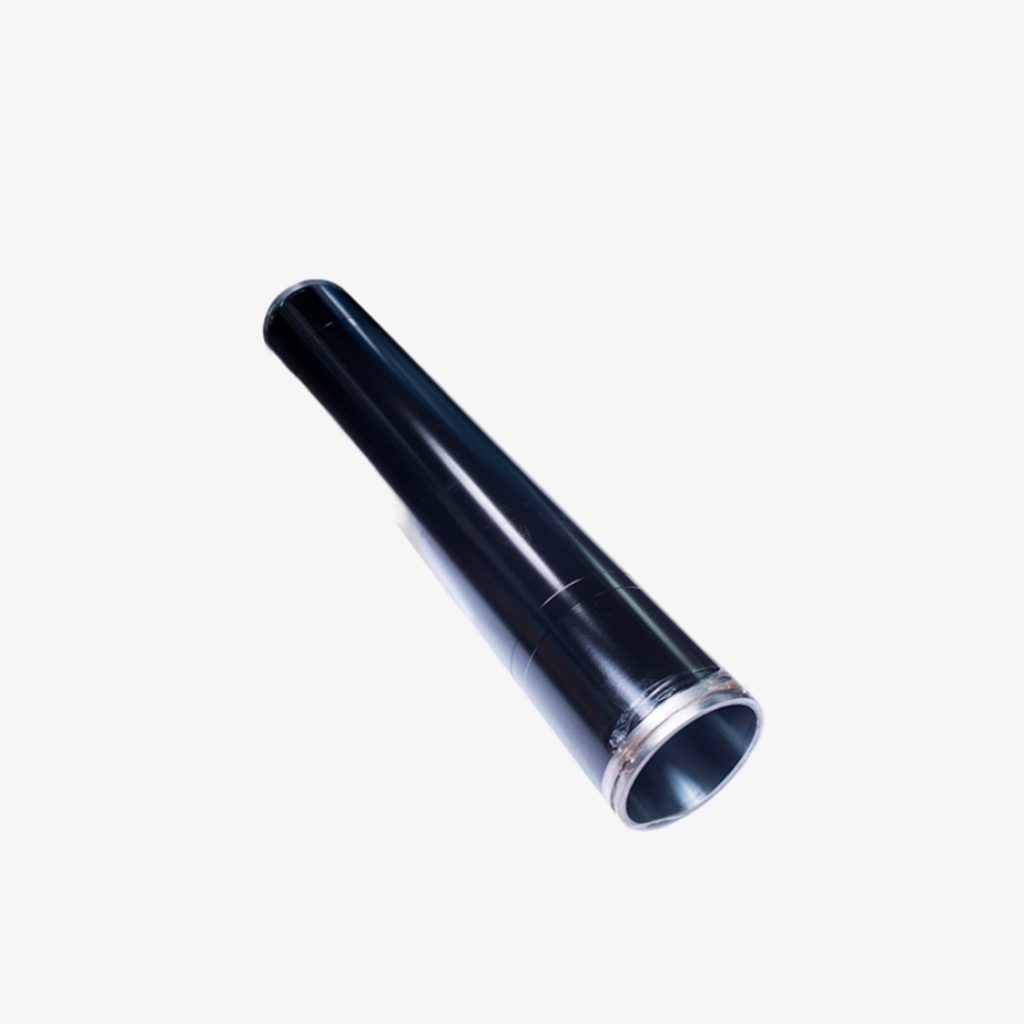
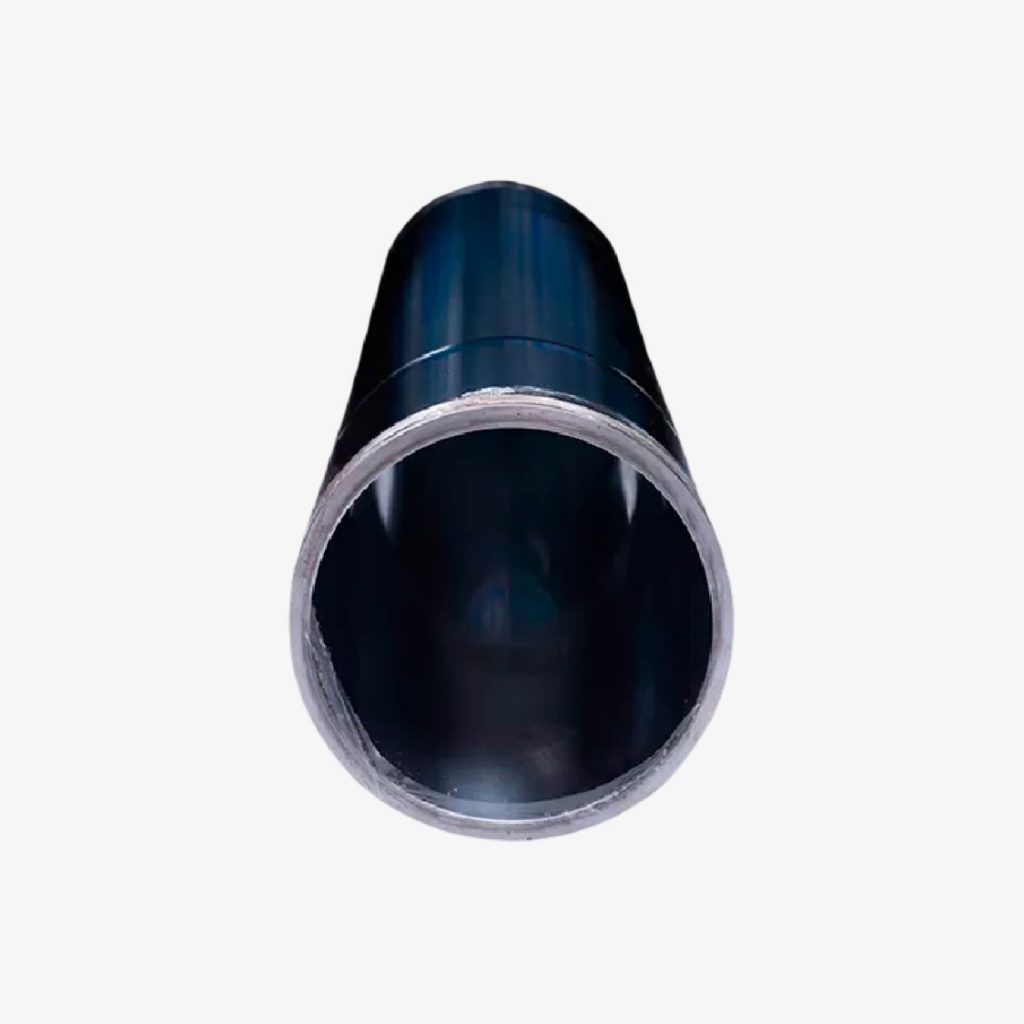
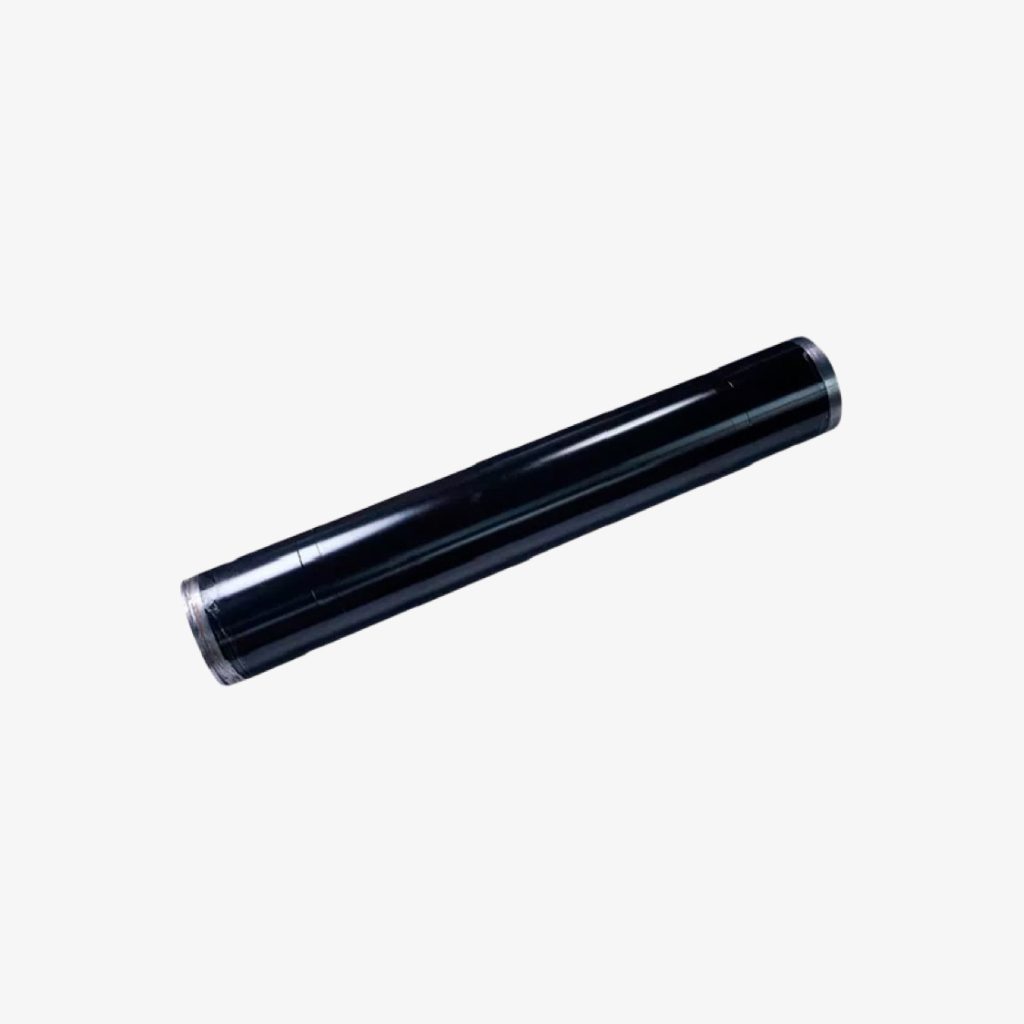
5. Hopper Components
Including blades, seals, and bushings, hopper parts absorb the brunt of coarse aggregates and cement paste during the loading phase.
- Replacement Frequency: Every 500–1,000 hours, based on concrete mix composition.
6. Hydraulic Hoses and Seals
These flexible components power the system’s movements. High pressure, age, and exposure cause degradation over time.
- Replacement Frequency: Inspect biannually; replace annually or when signs of wear appear.
The Hidden Cost of Wear Parts in Concrete Pump Pricing
Many first-time buyers focus on the base machine price, especially when comparing a boom pump to a trailer concrete pump. But without considering the ongoing cost of consumables, it’s impossible to calculate the true cost of ownership.
Some pumps may have attractive upfront prices but come with expensive or hard-to-find spare parts. Ask manufacturers about parts pricing, lifespan expectations, and availability. Choose brands with robust after-sales support and easy access to replacement parts to minimize long-term risk.
Proven Strategies to Extend the Life of Wear Components
Use Optimal Concrete Mix Designs
Concrete with too much aggregate or poor water-cement ratios causes accelerated wear. Stick to manufacturer-recommended formulas, such as C30 type concrete.
Train Operators Thoroughly
Experienced operators recognize the signs of wear and know how to avoid stress-inducing practices like dry pumping or abrupt pressure changes.
Commit to Scheduled Maintenance
Inspect critical parts weekly. Replace them proactively rather than reactively; planned downtime is always more cost-effective than a surprise failure.
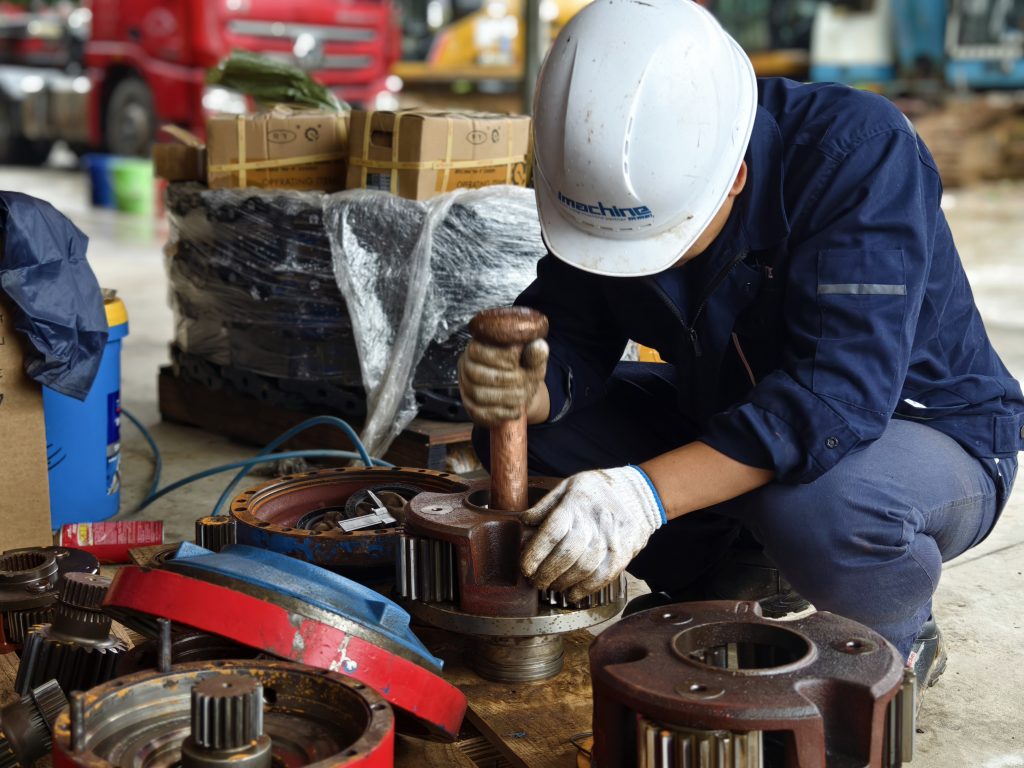
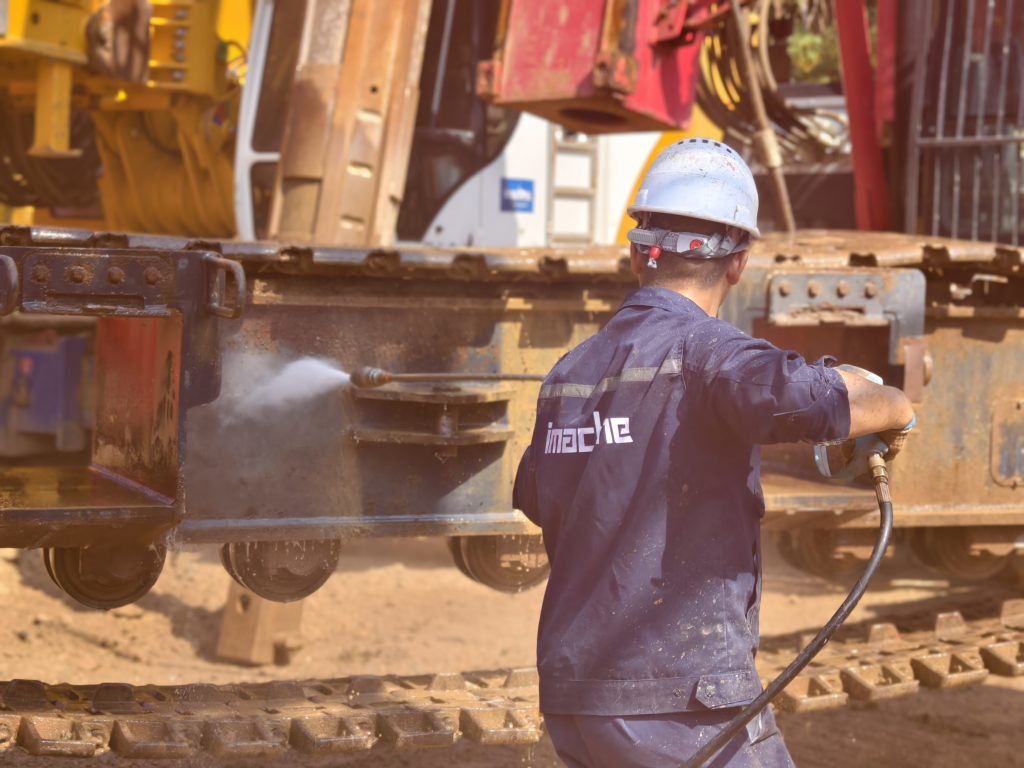
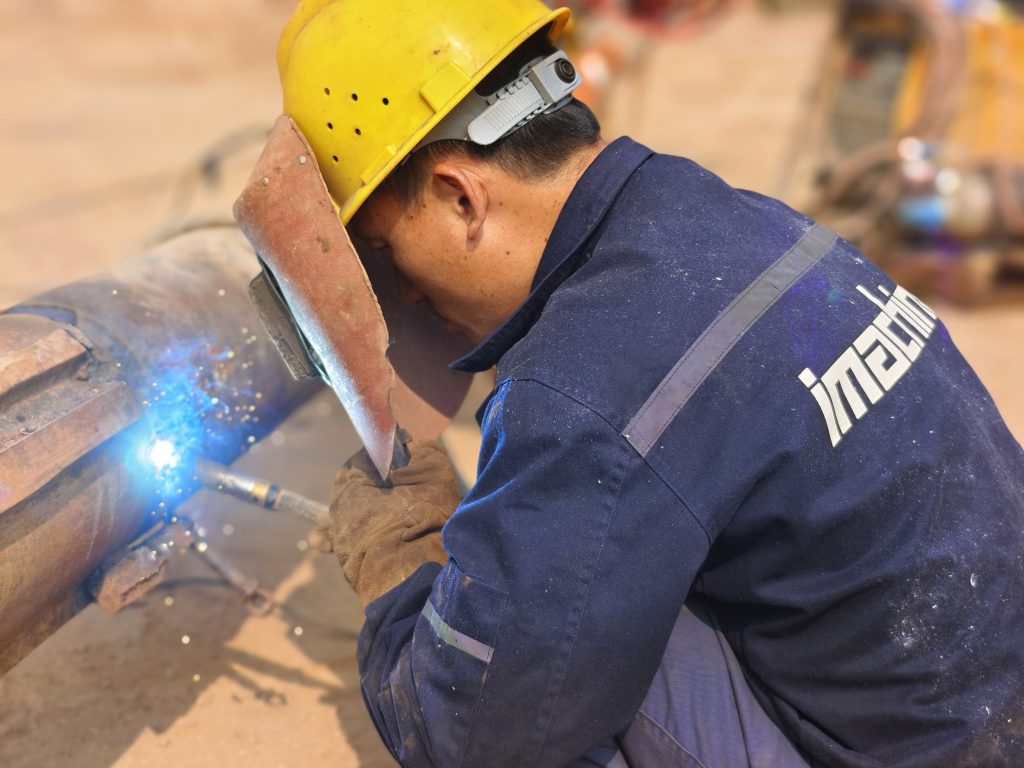
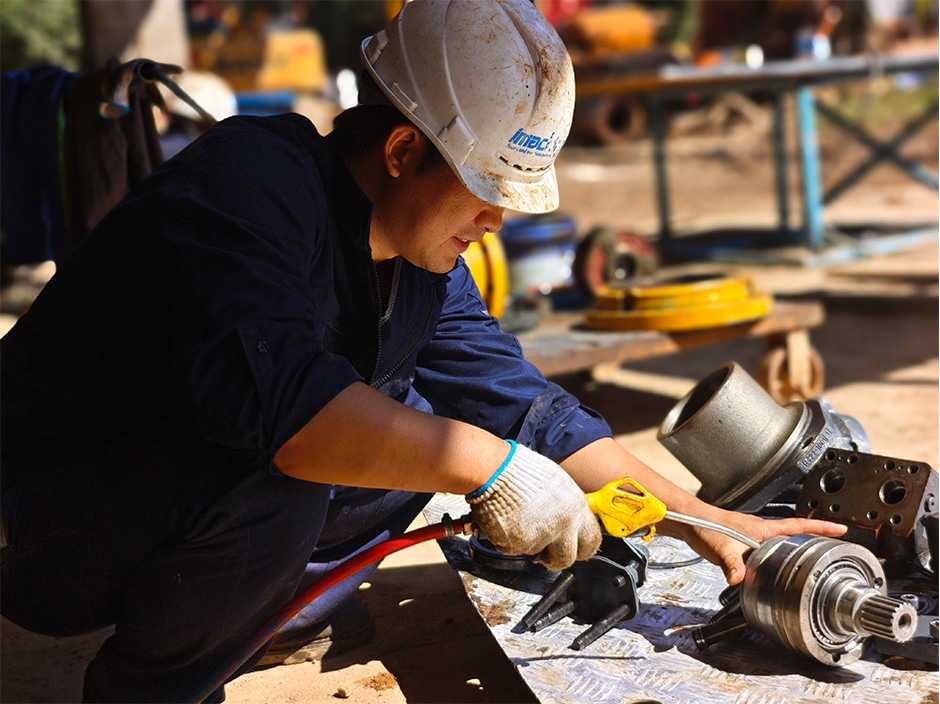
Conclusion: Monitor the Wear Part to Maximize the Value
Concrete pumps are invaluable assets in construction operations—but only when properly maintained. Knowing which parts wear fastest, how long they last, and how much they cost to replace enables smarter investment decisions and smoother job site performance.
Whether you’re managing a high-output fleet or operating a compact unit for small projects, never underestimate the influence of wear parts on your bottom line. Take care of the components, and the machine will take care of your worksite.
Contact imachine for Your Next Concrete Pump
At Imachine, we specialize in sourcing high-quality used construction machinery, including reliable concrete pumps suited for projects of all sizes. Whether you’re looking for trailer pumps, boom pumps, or spare wear parts, our team offers professional guidance and global delivery solutions tailored to your needs.
We provide detailed equipment inspections, transparent pricing, and dedicated after-sales support to help you make confident purchasing decisions. Contact us today to explore our latest inventory and discover how Imachine can keep your operations efficient, cost-effective, and ready for your next challenge.